Disc-Style Hand-Fed Drum-Style Hand-Fed Alternative Hand-Fed
Why Own A Bandit® Chipper?
Bandit chippers have been manufactured since 1983 and are known for their performance, reliability, efficiency, and durability. They retain one of the highest resale values on the market. For these reasons, it is easy to see why more industry professionals trust the Bandit name. Learn more in the following pages on how to sell the Bandit brand against the competition.
Features of Bandit Hand-Fed Chippers
Brush Bandit chippers contain many of the same attributes from model to model. This section outlines the important selling points and features that are found on Bandit chippers.
“Easy-Climb Spring Tensioning System”
The easy-climb spring tensioning system applies down pressure for the top feed wheel providing unmatched compressing power. The springs have four adjustments allowing for 300 to 660 pounds of down pressure (varies by model). With the springs in the lowest setting minimum down pressure is applied making it easier to feed larger diameter material with less limbs or branches. With the springs in the highest setting, maximum pressure is applied making it easier to collapse limby material into the chipper reducing trimming.
“Slide Box Feed System”
This unique system is featured on all units excluding the Models 65XP, 75XP and 12X, which feature a pivoting top feed wheel system. This slide box allows the top feed wheel to travel straight up and down with the flow and diameter of material passing through the feed system. This trouble-free system for carrying the top feed wheel applies direct down pressure for crushing material and through the spring tensioning system or the optional hydraulic lift cylinder.
The diagram below shows the slide box feed system on the right hand side and how it provide direct down pressure. The image on the left hand side is a pivot arm style feed system found on Morbark and some Vermeer models. The pivot arm does not provide direct down pressure and may cause material to wedge in the feed system.
In addition to the spring tension system a hydraulic lift cylinder is standard on most models (optional 9″ and select 12″ units). The cylinder is controlled by a handle located on each side of the infeed and hydraulically raises or compresses the top feed wheel. Depending on model this creates an additional 2,200 to 3,780 pounds of down pressure substantially increasing productivity.
“Dual Feed Systems”
A majority of the models feature dual feed systems. Each feed wheel is driven by high displacement hydraulic motors that will effectively pull material into the chipper reducing chainsaw work and operator fatigue. A bottom clean-out door is also included on dual feed wheel systems and extends knife life by allowing dirt and other debris to fall out.
“Synchronized Feed System”
Bandit’s feed systems feed material to the disc or drum at the rate the chipper wants to chip it. The natural feed rate of the chipper in feet per minute is determined by multiplying the chip length times the RPM of the chipper disc or drum times the number of cuts per revolution divided by 12. Because the hydraulic pumps drive off the engine, as the engine and disc or drum RPM drops, so does the speed of the feed wheels. Thus, the feed system is always in harmony with the chipper. Wood is never pushed against the disc or drum, which can cause a braking action and can heat the disc or drum, prematurely dulling the knives. And wood is never held from the chipper disc or drum, which can create fines and miscut chips. Bandit chippers produce the highest quality chips in the industry.
“Infeed Hoppers”
All Bandit chippers feature wide profile, heavy-duty infeed hoppers. Each hopper is standard with a 30″ fold down infeed tray that slopes 3 degrees making the chipper easier to feed. A safety control bar wraps around the sides and top of the hopper and controls the forward / stop / reverse functions of the feed wheels.
In lieu of folding infeed pan, a solid infeed with heavy-duty rim is optional. The HD rim assists with deflecting material into the infeed and is recommended when feeding larger diameter material.
“Discharges”
Each Bandit chipper features a discharge spout that can be adjusted in multiple directions. Most chippers feature a standard hand crank swivel and height adjustable discharge chute making it easier to rotate and adjust the height of the chute. A 3-position end deflector is also standard.
“Bandit Control Panel”
A Bandit programmed panel is included on all chipper excluding the 65XP and 75XP. This allows for consistency among all engine options, makes it easier to diagnose problems and display a wide variety of settings including engine parameters.
“Reversible Heat-Treated Chipper Knives”
The knives are the most important chipper component because they do all the cutting. The dual-edged knives used in all Bandit hand-fed chippers are made of high quality, heat-treated steel. Dual-edged knives have two sides to dull before needing removed and sharpened. Their high quality provides maximum life. All Bandit chippers (excluding the Model 65XP, 75XP and 12X) utilize four knives in lieu of a two-knife set up (used by some competitors) ensuring a highly productive, smooth cutting action and longer knife life.
“Engine Options”
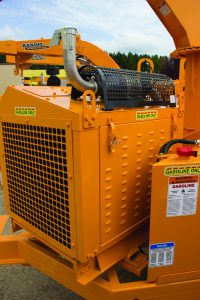
A wide array of gas and diesel engine options are available from most major engine manufacturers. Choose the power option and brand that matches the engines in your fleet of tree care equipment. Engines available from:
• Caterpillar • Ford
• John Deere • Kohler
High-Quality Paint Finish
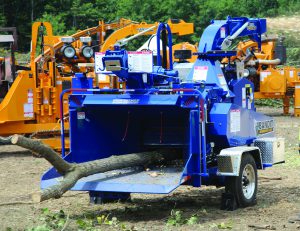
The best paint finish available for a chipper is provided on Bandit chippers. Bandit’s paint process features polyurethane paint and epoxy primer, which is better than powder coat (used by many competitors.) To provide a high quality paint finish, the process starts with pickled steel that is cleaned of impurities using a series of hydrochloric baths.
The machine is washed with high temperature alkaline cleaners and phosphoric acids. Through the process of cleaning, the surface is freed of oil and contaminants, which leaves an excellent surface for coating. The epoxy primer, which forms an impermeable barrier between the steel and moisture, is then applied. The chipper is then covered with a polyurethane paint. We use this paint process for our chippers because it provides the best finish available.
We understand that many companies are identified by their company’s colors. That is why we make it easy to purchase your chipper with the paint color of your choice. Two standard colors are available: Bandit yellow or green or a special color can be ordered for a nominal fee.
Safety Features on Bandit Chippers
Bandit chippers comply with all OSHA and ANSI safety requirements and also offer additional safety features that go above and beyond industry standards.
Please familiarize yourself with the safety features found on Bandit chippers.
Last Chance Cables
(STANDARD) These cables can be pulled to stop/reverse the infeed rollers in case of an emergency. Available on all hydraulic powered chippers.
Operator Safety Control Bar
(STANDARD) This control bar wraps around three sides of the infeed chute and controls the forward / stop / reverse functions of the feed wheels.
Shear Bar
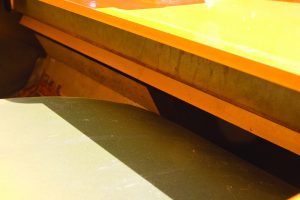
(STANDARD FOR DRUM CHIPPERS) The Shear Bar takes the form of a cross cutting bar that spans the full width of the drum, and is mounted in the upper portion of the drum housing, providing a secondary anvil for the knife to cut against.
Wooden Pusher Paddle
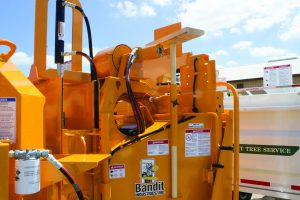
(STANDARD) This device helps the operator feed small wood debris that may tend to lie inside the infeed hopper.
Safety Decals
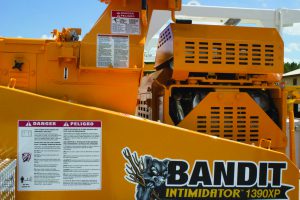
Prominently displayed and available in multiple languages. Spanish/English combination now standard.
Chipper Hood Pin with Pad Lock
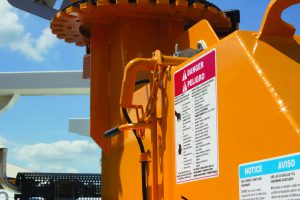
(STANDARD) Prevents the disc’s hood pin from being removed when the disc is turning. (The disc’s hood won’t open until the disc has come to a complete stop).
Electronic Limit Switch on Disc & Drum Hood Pin Lock Out
Prevents engine from being started without the hood pin in place. Someone turning the key cannot inadvertently start the engine, disc or drum.
Manuals and Videos
Supplied with each unit (operations, service, parts, safety).
Ergonomic Design:
• Low risk positions for any operator
• Low force, low stress operation
• Less lifting required to feed a Bandit chipper
• No repetitive motion functions
required for operation
• Easy to read gauges
Popular Options For Bandit Chippers
Many options are available on Bandit chippers. The following section describes some of the most popular options available on these machines.
Hydraulic Tongue Jack
This feature hydraulically raises and lowers the chipper’s tongue and hitch. It eliminates manual labor of hand cranking, and is especially popular on our heavier chippers.
Knife Saver
This hand-held knife sharpener touches up knives in the chipper. The diamond wedge inside the Knife Saver will put a sharp point back on a dull chipper knife while the knife is in the chipper, reducing the frequency of changing knives. Sharp knives lower fuel consumption, reduce vibration and improve chip quality.
Hydraulic Winch
This feature is used to pull large material and bundles of material that are too heavy to carry by hand to the chipper. This useful option can eliminate a tremendous amount of trimming and chainsaw work, especially when processing large material. It can also reduce the labor associated with the chipping brush by moving bundles of material from a distance to the chipper.
Knuckle Boom Loaders
Loaders work great for feeding larger diameter trees branches or small piles of brush. The Model 21XP equipped with a Kesla loader increases the versatility of this unit.
Rubber Track Undercarriages
(Steel tracks available for certain models)
A variety of hand-fed chippers can be equipped with a rubber track undercarriage. These units are great for small land clearing jobs, fire prevention, and right-of-way clearance. The radio remote controls the following functions: track forward/reverse, track left/right, discharge left/right, discharge deflector up/down, yoke up/down, track low/high, engine e-stop, and hydraulic winch if applicable.
Hydraulic Bottom Bump Bar
(OPTIONAL) When force is applied to the bump bar, the feedwheels stop. The device functions mechanically, not electronically, through a linkage that diverts all the hydraulic power away from the feedwheels by stopping or reversing the feed wheel when activated. Note: the bottom stop bar is NOT sold as a safety device and goes above and beyond all ANSI and OSHA chipper safety requirements and is therefore an an option for Bandit chippers.