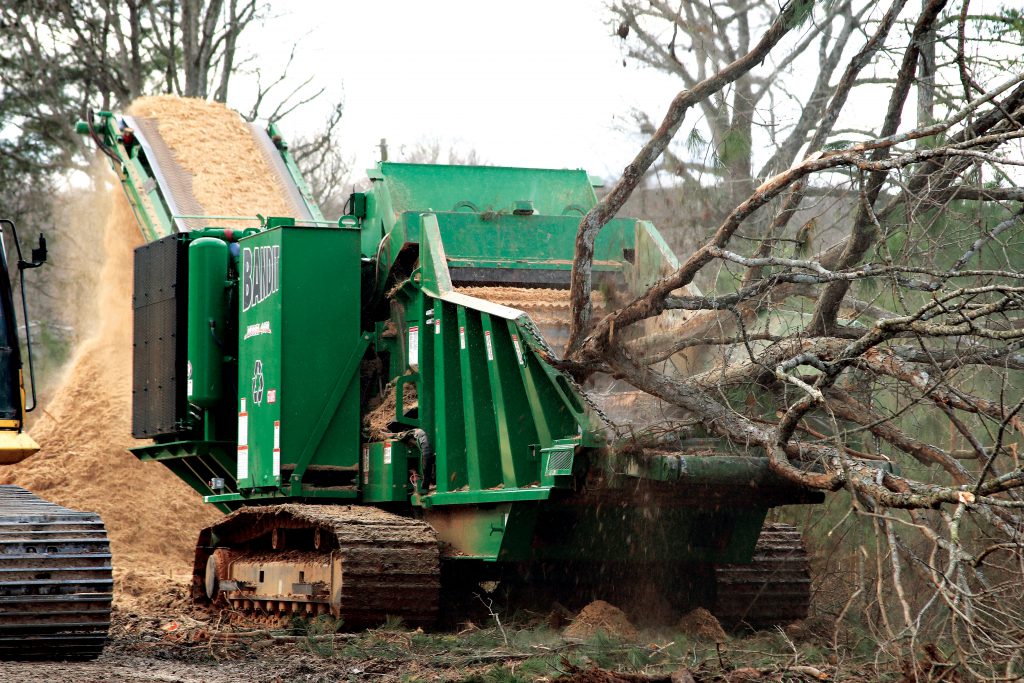
1425XP 1680XP 2460XP 3680XP 3680XP Track 4680XP 4680XP Track HM6420 Track
Why a Bandit Horizontal Grinder
Bandit Horizontal grinders will process an amazing array of material, such as stumps; logs; brush; wet leaves; whole trees; landscape waste; pallets; telephone poles; sawmill; logging; chip and paper mill by-products; shingles; plastic pile and more.
CUT IT, CHIP IT, OR HAMMER IT with a Bandit horizontal grinder! Which grinding method is best suited and preferred for your customers applications?
“CUT IT”
Bandit’s “Beast” models feature a unique cuttermill designed to cut material apart. Since the cutting action is much smoother, vibration is minimized resulting in reduced wear-and-tear on the machine. Each cuttermill features cutterbodies that are attached to heavy-duty support arms regulating the cut, creating an efficient cutting action. The cutterbody utilizes a raker positioned ahead of the tooth limiting the cutting depth to approximately ¾”. This process correctly sizes material on initial cut and allows material to immediately pass through the screen and exit the grinding chamber. By grinding this way, each machine relies less on the screen and gate to size material reducing the overall wear on the screen and gate.
A wide variety of cutting teeth are available for the cuttermill to effectively process a diverse range of material. These teeth are either 1” or 2” wide depending on the mill set-up. Select models are available with a “fan” style tooth assisting with pushing material through the screen, increasing production while reducing wear on the cutterbody.
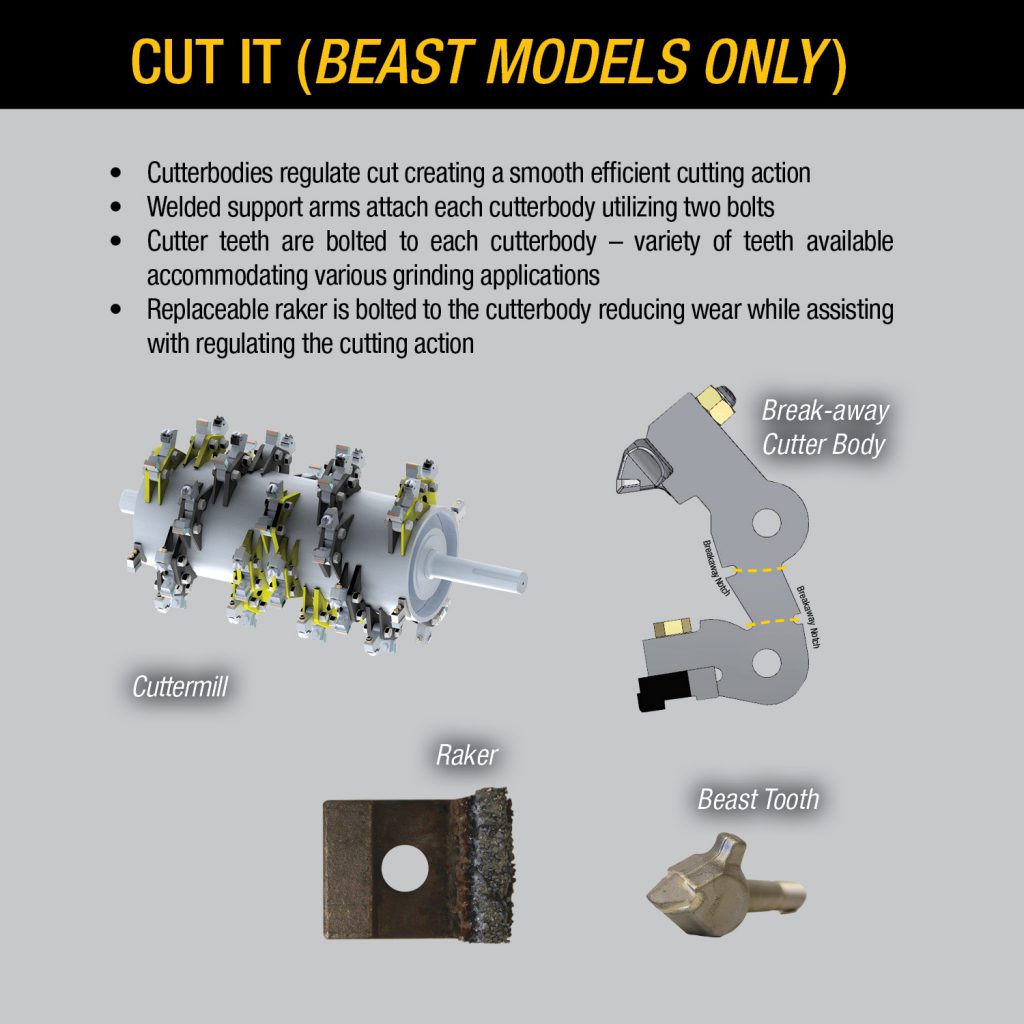
“CHIP IT”
All “Beast” grinders are capable of producing a dimensional chip with a chipper knife set-up. For those needing a fine chip of approximately ¼”, knife style cutterbodies can be ordered for the cuttermill and are equipped with a small knife. This set-up can also be easily converted back to teeth to go back to normal grinding. For larger chips sizes ranging from 5/8” to 2”, a dedicated 4 or 8 knife chipper drum is available on select “Beast” models. When a grinder has the chipper knife set-up, only clean round logs should be ran through the grinder.
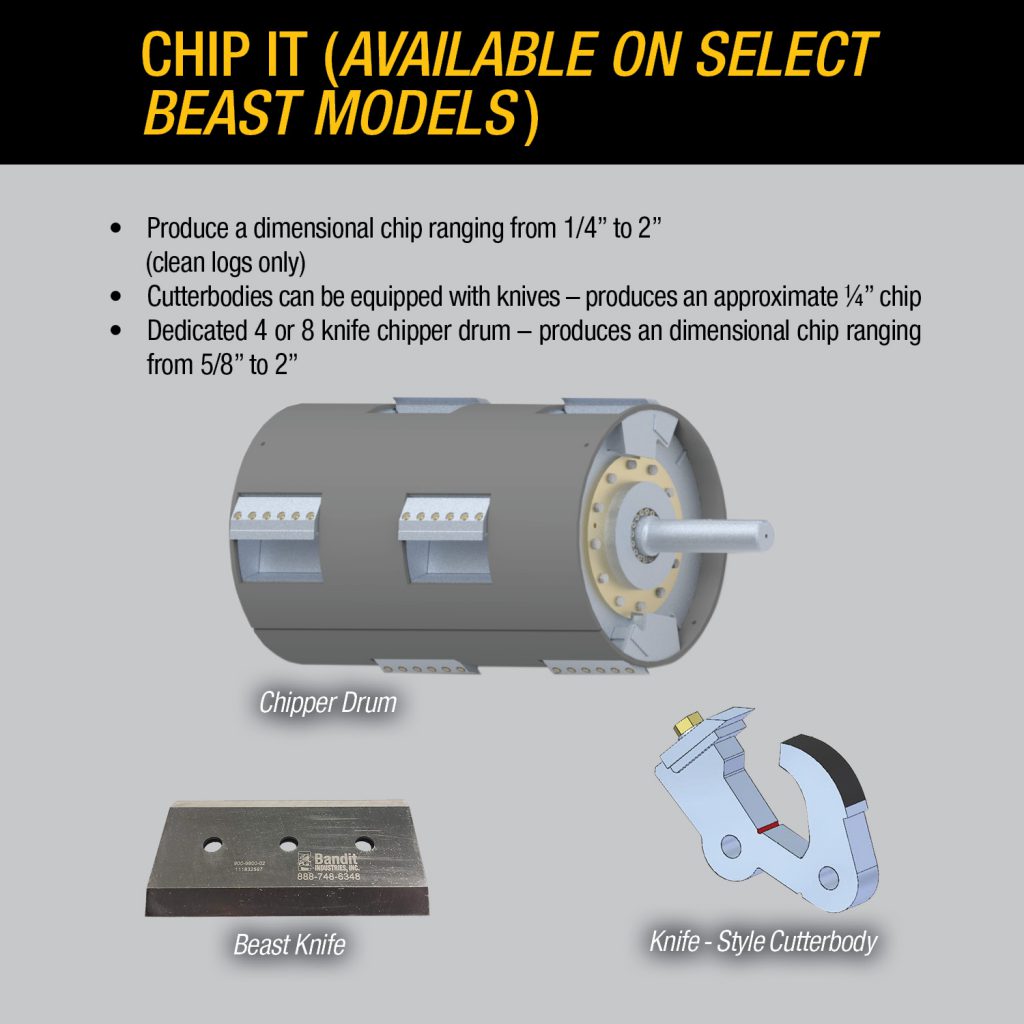
“HAMMER IT”
In 2024, Bandit introduced its first hammermill grinder, called the HM6420. With considerable research and collaboration, the Bandit team was excited to bring this highly productive 45” capacity grinder to market. This machine was designed and manufactured to accommodate those grinding applications that may contain contaminants. A Caterpillar C32, 1,200 horsepower engine provides ample torque and horsepower for optimal machine performance and productivity.
The heart of the HM6420 is a 50” diameter x 66” wide hammermill. The heavy-duty mill features 1.75” drum skin custom formed from rolled plate. The drum is supported by a 7” main shaft constructed of alloy steel that has been ultrasonic tested. Each pocket within the drum is manufactured from high strength A-514 steel. These combinations create a structural sound mill for added durability and integrity. The mill is equipped with 20 carbide infused hammer inserts built to withstand the toughest material fed into the machine. Each holder is securely attached to the mill via a patent-pending quick change pocket system. Each holder recesses into the mill pocket, increasing durability. A top plate covers the pocket and held in place by six hex bolts. The hammer insert is attached to each holder utilizing two bolts. With this set-up, the mill hardware is easier and quicker to replace.
An impact detection system is standard and designed to limit damage if a contaminant is struck inside the grinding chamber. Once an impact event is detected, the grinder will idle down, open the gate, disengage the clutch, and reverse the feed.
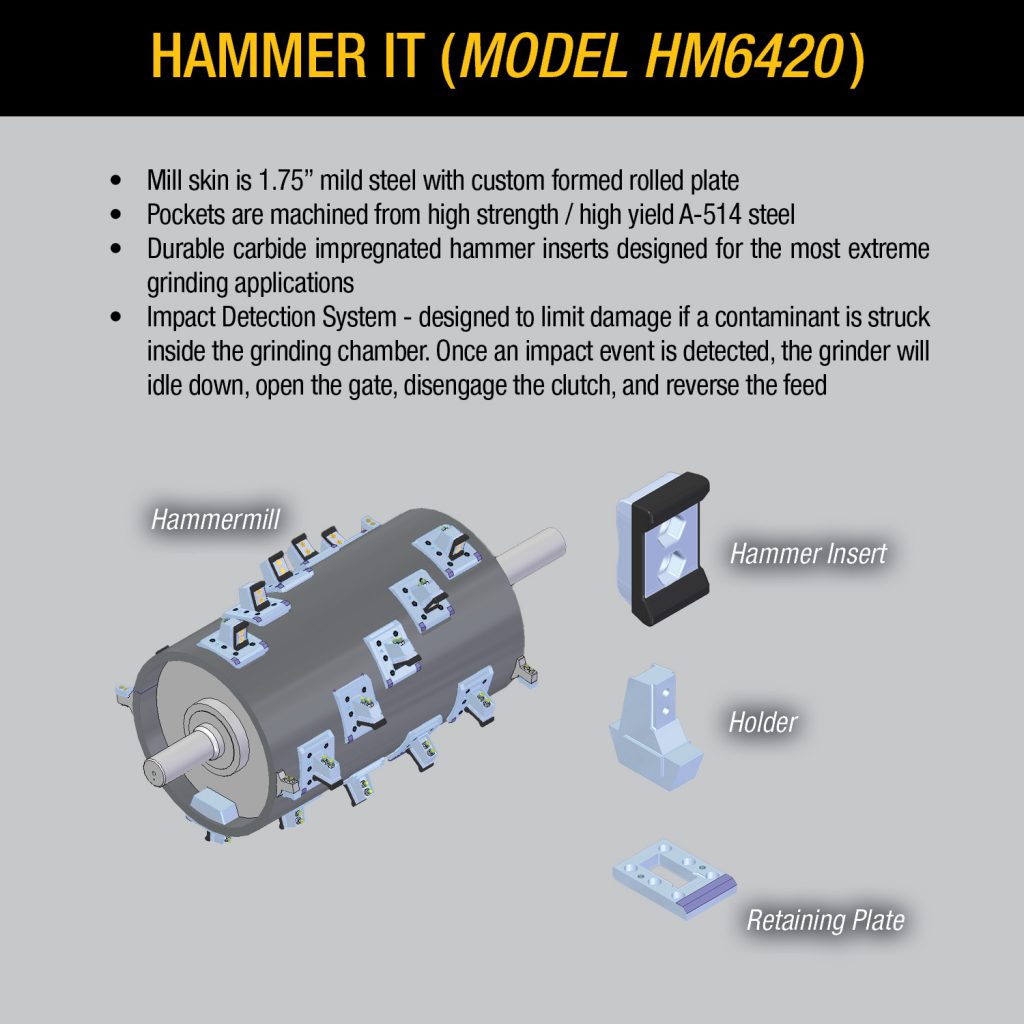
Powerful Horizontal Grinders
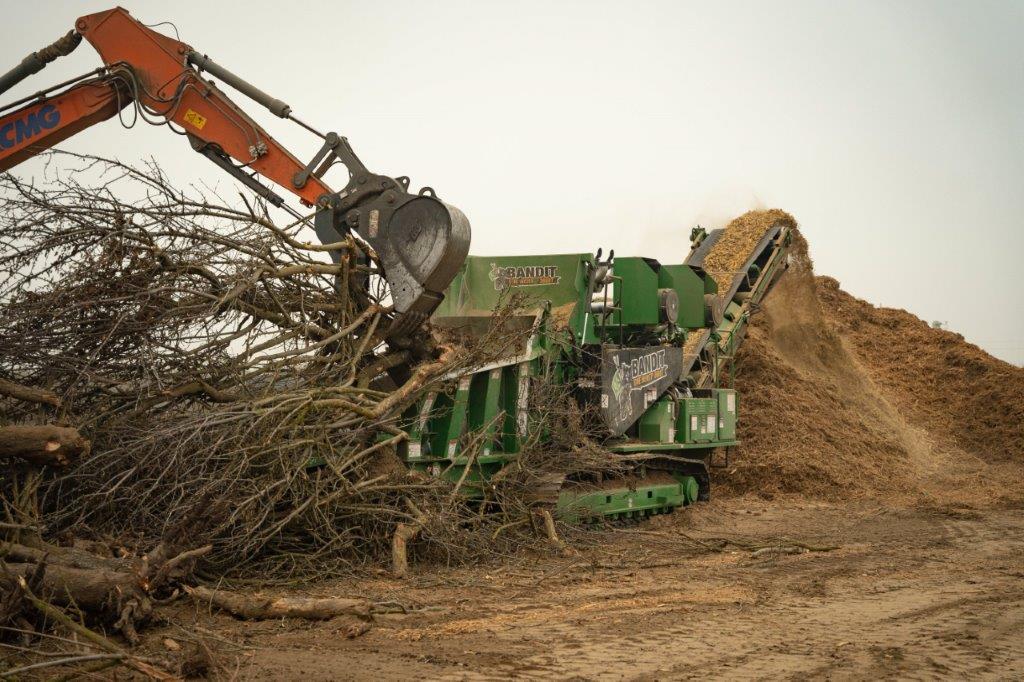
Bandit grinders have been in service and continually improved upon since 1995. Like all Bandit equipment, These grinders are built by specialized teams using the highest-grade components and extensive welding to produce a reliable machine capable of handling daily high production grinding. A variety of models are available ranging from 14″ to 45″ capacity and engine options up to 1,200 horsepower.
Large Diameter Mills
Mills on the Bandit horizontal grinders are generally larger in diameter compared to most competitors. These larger diameter mills turn at a slower RPM generating more torque, requiring less horsepower and fuel during grinding. Additionally, the machine will vibrate less reducing stress on the machine and its components.
Mill Options
Below is a listing of the mill options by model:
*** 1425 – 14 tooth – cuttermill
*** 1680 – 26 tooth – cuttermill
*** 2460 – 30 tooth – cuttermill
*** 2680/3680 – 30 or 60 tooth – cuttermill
*** 4680 – 48 tooth – cuttermill
*** HM6420 – 20 inserts – hammermill
Downward Cutting Mills
All Bandit grinder mill turns downward, cutting against a one-piece infeed chain which serves as a moving anvil on the models 2680 on up. This system provides tremendous benefits over the competition (Morbark, Peterson, and CBI / Terex) – the downward cutting action produces a more uniform product because material is less likely to turn or roll. The rotation of the mill pulls material towards the mill and works in conjunction with the infeed conveyor and feed wheel. Mills that turn upward, tend to push material away from the infeed conveyor and mill, and actually fights against the feed system. The downward cutting action is more aggressive, allowing the entire feed system to provide a positive control of the material going through the machine. This downward cutting action also uses gravity to hold material in place for processing, and further helps to reduce vibration.
There are many other advantages to our down-turn mills. Upturn mills on competitive grinders cut against a fixed anvil, forcing material away from the mill. Upturn mills also cut against an anvil positioned in the upper part of the grinding chamber. The material wants to tumble or fall from the anvil and most of the material is ground against the feed wheel. There is not a controlled breakdown at the anvil or feed wheel thus most of the material is sized in the screening chamber which yields a less uniform product, takes longer to process the material, reducing production while increasing screen wear. With a Bandit grinder, more material is cut-to-size on the very first pass through the mill allowing it to pass through the screen limiting time in the grinding chamber.
From a safety aspect, upward turning mills on alternate brand machines are much more likely to throw material violently from the machine, creating a potential safety hazard.
Augers
Augers are utilized to assist with moving material and prevent spillage. The models 2680, 3680 and 4680 have augers as standard. The augers are located in a auger box and has a bottom clean-out door for easy cleaning. Pressure transducers sense when the pressure is at relief / stall and reverse the augers to clean out material.
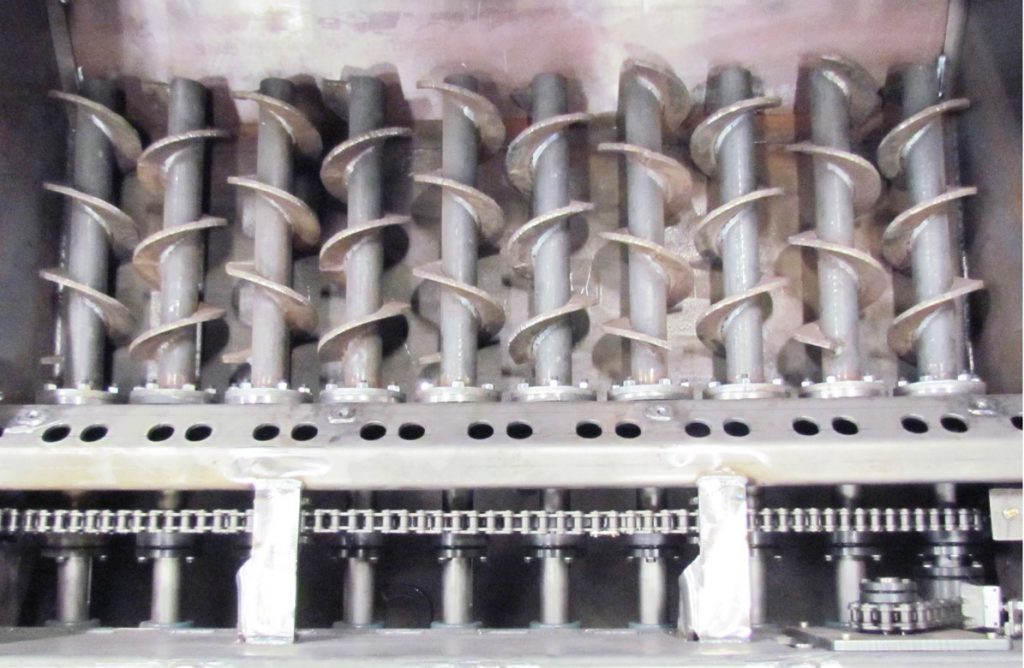
Accessibility
The infeed slides ahead on the 2680, 3680, and 4680. This feature moves the conveyor several feet away from the cutter head, allowing easier access to the cuttermill and debris augers for service and maintenance. No other competitive grinders have this feature.
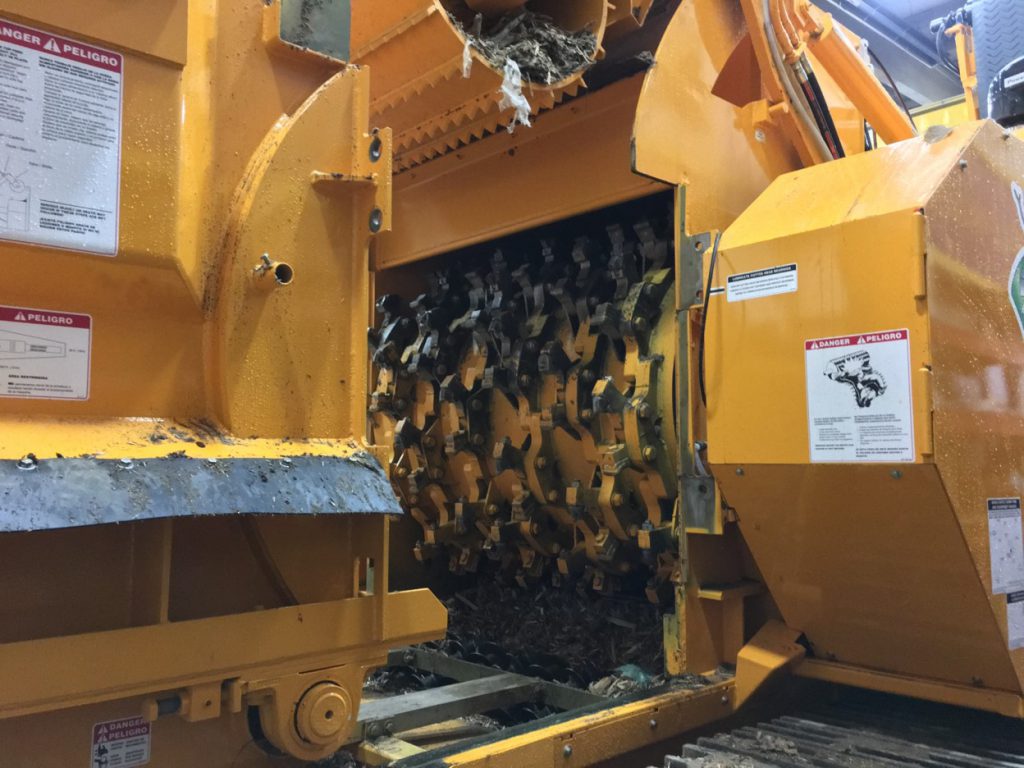
Screen and Gates
A wide variety of screen options are available ranging from 5/8″ to 7″ hole sizes. Below are the various configurations available:
Diamond Screen: provides highest production rate with with a less consistent end product.
Round Screen: is good for dry material and regrind / coloring. Creates a more consistent end product compared to a diamond screen, but will be less production.
Square Screen: Creates most consistent end product with lowest product rate.
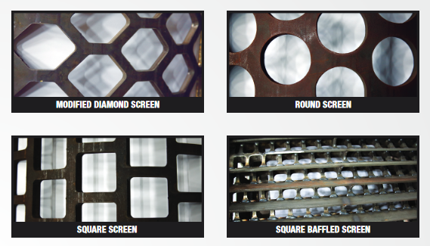
The Screen(s) and gate on 2680, 3680 and 4680 are changed from inside the grinding chamber, while the 1425, 1680 and 2460 the screen(s) are removed from the side of the machine. Due to the cutting action of the Beast (which relies less on the screen/gate to size material) the screen and gate are generally constructed of thinner material and still last up to twice as long compared to competitive units.
Hydraulically operated gates are standard on the 2680, 3680, and 4680 and can be opened / closed by the radio remote control. If the operator hears a metal object they can open the gate allowing the object to exit the grinding chamber quicker reducing damage.
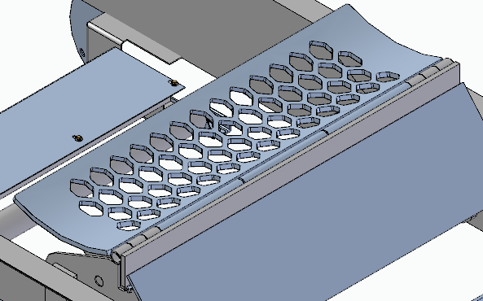
Heavy-Duty Infeed Conveyor
The WDH120 infeed conveyor chains are designed to handle heavy material being loaded and carries material with less spillage. Featuring 1/2″ thick A36 steel with a 3/8″ angle iron support. With the unique way the angle iron is welded to the slat, it gives two points of contact to evenly distribute the weight of the load on the infeed chain. The rugged construction of the infeed, coupled with the fact that it’s always moving, means the infeed will last for years.
Since the mills on all Bandit grinders cut downward the infeed conveyor acts as a moving anvil on the model 2680’s on up. Morbark, Peterson, and CBI/Terex all use drag style chains causing increased spillage and are more difficult to replace / change
If a slat is damaged on a Bandit grinder infeed chain, that single slat can easily be removed by tapping the pin out from the side of the infeed.
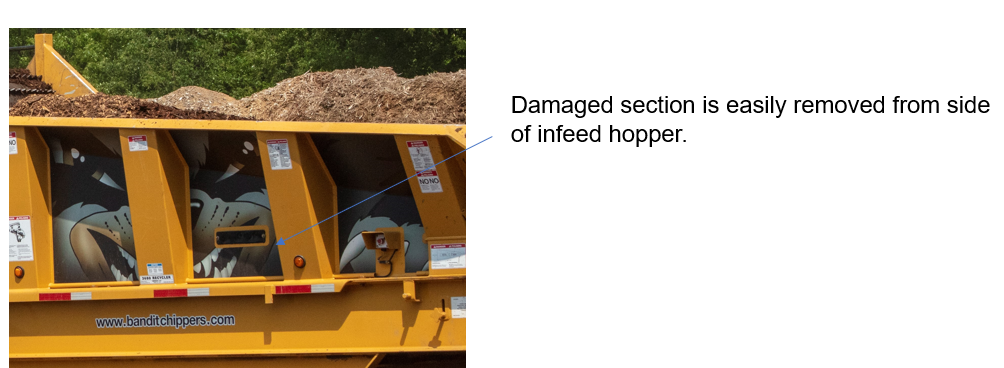
A heavy-duty feed wheel is located in front of the mill and assists with pulling material into the mill. Feed wheel forward, reverse, and up functions of the feed wheel are all controlled by the standard radio remote control.
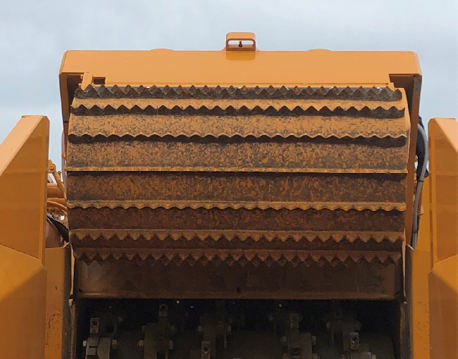
Height Adjustable Discharges
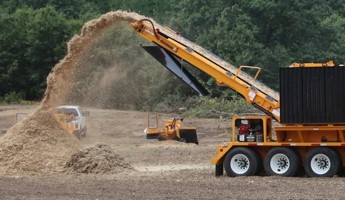
All discharges excluding the 1425’s, 2460 and HM6420 track models are height adjustable. Each of these discharges have a magnetic head pulley at the end to separate nails and other metallic debris. The discharges are 2-3 speed and 48-56″ wide to help spread out material exiting the grinding chamber.
Radio Remotes
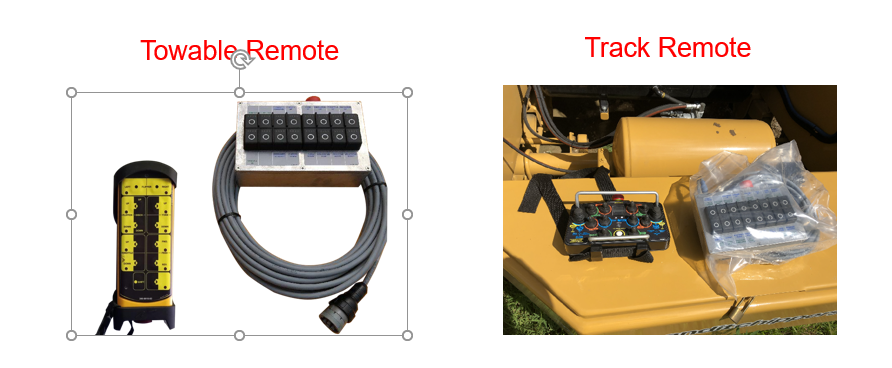
Each grinder with the exception of the Model 1425 is standard with a radio remote control and tether back-up. The remote will control the infeed conveyor, feed wheel, discharge functions, track functions (if applicable), hydraulic gate (on select models) and engine e-stop
Bandit Control Panels
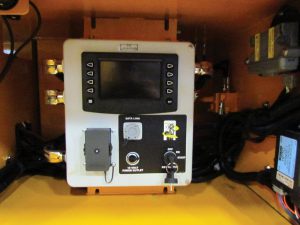
Bandit’s control panels are standard on each Bandit grinder and are programmed at Bandit allowing for consistency among a variety of engine options and make it easier to diagnose problems. The panel will display a variety of settings.
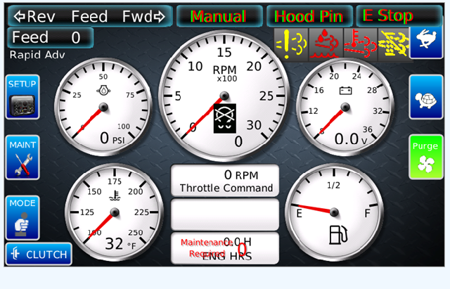
Also standard on all models excluding the 1680 is a multi-speed proportional feed system. A proportional drive adjusts the speed of the infeed to the engines RPM providing a steady flow of material to the mill without having to stop and back material out of the mill via the auto feed maximizing production. The promotional drive will produce a finer product. If the product is too fine the proportional drive can be shut off allowing the auto feed system to control the flow of material to the mill.
Stress to your customer the benefits of the proportional feed system, including fuel savings, extended drive belt life, and longer life on wear parts due to consistent load.
Dust Suppression System
This feature wets down material that is being processed. Spray nozzles are located above the feed wheel of the grinding chamber, and over the discharge conveyor. They can spray a combined total of 7-½ gallons of water per minute at 40 PSI: 1-½ gallons per minute on the nozzles at the top of the feed wheel, 1-½ gallons from each of the sides, and 3-½ gallons sprayed on the discharge conveyor. Applying water to the material in this manner suppresses dust in dry grinding conditions, and it’s especially critical when grinding shingles to prevent liquefying and tar balls. Applying water is also essential when coloring mulch with the Colorizer attachment.
Popular Options for The Beast Models only®
Set Up Your Beast For Your Application As with all Bandit products, a wide variety of options are available for The Beast horizontal grinders. There are a wide variety of options that give the Beast the ability to process such a wide variety of materials and produce such a wide range of valuable end products. The nice thing is that should your markets change most of these options can be added to the Beast to provide you with the ideal machine for your situation.
Color Max Coloring System
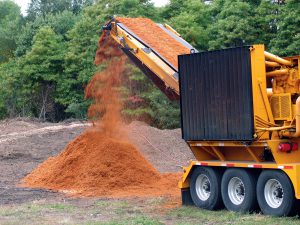
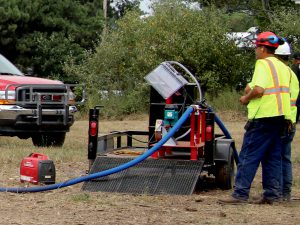
Adding the coloring option converts the Beast into the best coloring machine on the market. Not only will it out perform other grinder/coloring systems but it will also out perform stand alone coloring systems. The liquid colorant system evenly coats mulch with pigment while it’s being processed. With the Color Max system installed, a 755-HP horizontal grinder can color as much as 300 cubic yards/hour during the final grind, depending on the desired product size.
The Beast coloring system will produce more colored mulch per hour using less water and colorant than any other grinder/coloring system or any other stand alone colorizer. An added bonus is that there is almost no colorant spillage from the machine and no mess to deal with. The flow of colorant is easy to adjust, and automatically adjusts with the flow of material into the mill. The cuttermill in The Beast does a great job coloring mulch – the large-diameter mill with cutterbodies that extend out serve to stir and mix the wood with the colorant, delivering an excellent colored mulch, with great coverage.
The Beast®, Electrified
For those looking to grind in a consistent setting or inside a building an electric Beast may be a viable option. The Beast with electric drive motor is an economical and cost effective option to a diesel powered machine. All electric grinders are simple to set up and require less maintenance compared to a diesel engine. Each electric motor comes with soft-start, which reduce the incidence of line-voltage drop. The electric motor options are crusher-duty motors from WEG, the largest electric motor provider in the world with global service support. It is customers responsibility to provide proper electrical requirements and to hook machine to electrical source.
Cross Belt Magnet
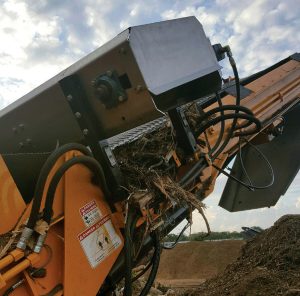
This optional powerful magnet mounts over the discharge conveyor and helps to remove steel from the end product, especially in pallet and C&D grinding.